BIRMINGHAM, UK, Mar 24, 2015 - Delcam has added a number of new options for reverse engineering to its PowerSHAPE Pro software for the design of products and tooling. The 2015 R2 release of the software also includes improvements to speed up and simplify the editing of product designs to make them more suitable for manufacture.
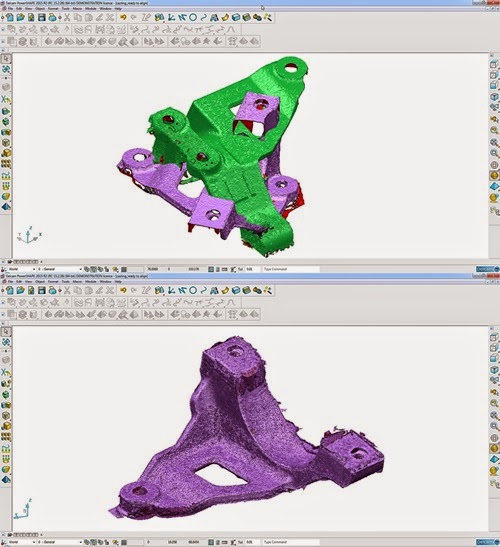
By offering a combination of solid, surface and direct modelling, together with reverse engineering, PowerSHAPE Pro provides the most comprehensive range of design techniques available in a single CAD program. Having all the different technologies in the same package reduces the need to transfer data between multiple programs and so streamlines any product-development process that requires both reverse-engineering and CAD functionality.
PowerSHAPE Pro can connect directly to most scanning hardware to capture and display scan data in real time. The 2015 R2 version includes a new split-screen alignment option that makes it quicker and easier to combine multiple scans, taken, for example, from the opposite sides of a part. The new method also allows more accurate snapping of alignment points, giving greater accuracy in the resulting single CAD model.
PowerSHAPE Pro can be used to take cross-sections through the scan data to generate wireframe for the development of surface models. The wireframe can be simplified automatically into lines and arcs, reducing the number of points needed to describe the item and giving more precise geometry for the re-engineering of the model.
Another new option is the ability to morph a complete solid or surface model to a mesh. This can be used to compensate for spring-back when pressed parts are released from their tooling. Morphing can be used to update a nominal CAD model to match the part as it is made in reality or to modify the surfaces of the tool so that the part can be produced in the desired shape represented by the CAD model.
On the modelling side, analysis of models has been made easier as the Smart Feature Selector now displays the type and parameters of each feature interactively as the cursor is moved around the model.
In addition, the ability of the Smart Feature Selector to find, select and edit multiple similar features has been extended. Now, any number of items of the same type, not just similar features, can be edited in a single operation. For example, all the arcs within a model could be set to the same diameter or all the holes could be made the same depth.
Two enhancements have been made to the tools for the creation and editing of curves. Firstly, the Composite Curve tool has been more efficient so that it needs fewer clicks to create the curve, even when following fragmented edges. Secondly, the Re-point dialog now displays the deviation between the original curve and the new one, and it is also possible to re-point a curve to a known tolerance. This makes it even easier to create high-quality, smooth surfaces when re-engineering scan data or when re-modelling an existing design to allow it to be manufactured.
No comments:
Post a Comment